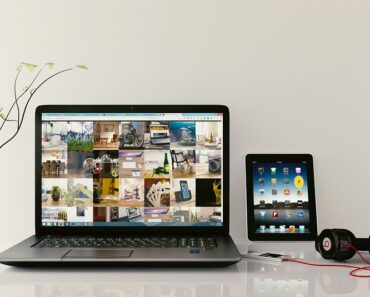
5 reasons why Diblister tablets and capsules are from plastic packaging
Why deblister?
Q: Why are tablets and capsules removed from plastic packaging?
Improve production yield…
a. In each blister packaging line, a certain amount of blister packaging produced during or after production will be rejected for the following reasons:
Often, during bubble filling, the filler of the product momentarily jams, leaving the pocket empty. The device detects this and rejects the bubble after sealing
shoddy print
Wrong batch number
The expiration date is wrong
Wrong materials were used
Often, a recovered disc can be returned to the line for a refill.
Q: What are the alternatives to deregistration?
Dispose of waste packaging properly which means you lose product value and incur maximum waste disposal costs.
Separate packages and product by hand and dispose of them separately.
Q: Why not just improve the performance of the blister packing line?
A: Blister packaging is often made to an optimum specification of 95%. Considering the time and costs involved in adjusting the machine to get that last 5%, it is easier and more logical to incorporate a separate process using a PRESS-OUT registration removal machine.
Also, no matter how efficient a blister packing line is, every time the machine is started for a new batch, an initial trial run with a live product results in many rejections. Often, good blister packs produced in a test run cannot be marketed because they do not form part of the validated production batch.
These incorporation denials are unavoidable, and because they create large amounts of rejections, deregistration is still a very useful procedure for handling incorporation denials alone.
Waste reduction…
Q: Can you dispose of waste chips in the regular paper trash?
A: Yes. In fact, many businesses make huge savings with this app alone. It is very expensive to pay for incineration or disposal of the active product, and of course, if the filled bubble is incinerated, the company pays high rates for unnecessarily burning large air spaces and packaging materials.
Improve operator motivation…
Q: Isn’t it cheaper for employees to squeeze out blisters by hand?
A: Recovering 50,000 blisters by hand costs about $16,650 in labor costs alone. The job is painful for operators, can lead to repetitive stress injuries, is very unmotivating, and is a wasteful use of human resources.
Where a fully automatic machine is not justified, there are small scale manual machines available which can allow registration to be removed at a rate of up to 30 blisters per minute.